High speed steel drill bit sharpening when drilling various materials
Views : 419
Update time : 2017-04-20 20:11:37
When using a high speed steel drill bit, it is unreasonable to use it without any sharpening of the cutting edge (vertex, cross blade, rake angle, rear angle, etc.), or no purpose, no requirement. To make the best use of the material must be processed according to the different nature of the drill bit different grinding, so as to make the drill really play the desired effect.
Drill bit before grinding must understand the structure of the drill bit and the characteristics of the material being processed and the contradiction between the two, to understand the problems arising in the drilling, so as to be targeted to sharpen, solve the problem.
First, the processing of different materials generated problems and solutions
1. Cast iron a low hardness (usually 175-250HB), low strength, brittleness, plastic deformation is small, low thermal conductivity, the organization is loose, the chip into a crushed, drill bit wear almost all in the back, The maximum, hinder the tool life and production efficiency.
For the above questions can be the following approach:
A. The drill bit is easy to wear at the corner of the double vertex angle, so it is easy to wear and form a double vertex (see Figure 1), which increases the drill life by 1 to 2 times.
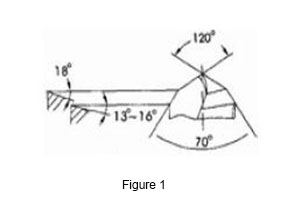
B. Appropriate increase after the angle. The outer edge of the rear edge of the use of 13 ° ~ 16 ° to reduce friction, improve the life of the drill bit.
C. Drilling to increase the feed, and appropriate to reduce the cutting speed, but not the use of high speed and small feed.
D. If the use of coolant, must not be intermittent use, while the flow should be appropriate, otherwise, the amount of small and intermittent will cause local hardening of the hole, and powder chip grinding edge will also accelerate the drill wear.
2. High-strength steel such as tool steel, carburizing steel, spring steel, bearing steel, heat-resistant steel. Drilling, drill bit cutting edge wear faster, shorter life.
For the above questions, the following approach can be used:
A Selection of high-performance high-speed steel or carbide production of the drill.
B. For hard and brittle steel, the front edge of the outer edge of the drill can be reduced to increase the strength of the edge. For steel that is hard and plastic, it does not have to be reduced.
C. Vertex angle can be used around 118 °.
D. Use phosphorus-containing cutting oil as coolant.
3. Stainless steel - generally martensitic, ferrite and austenitic three types of stainless steel. Martensitic stainless steel can resist atmospheric corrosion, good mechanical properties, the quenching and tempering treatment can improve the cutting performance, if the hardness is higher than 30HRC, the drill wear faster. Ferritic stainless steel chromium content than martensitic stainless steel, so heat treatment can not be strengthened, the cutting performance worse than the martensitic stainless steel. The mechanical strength of austenitic stainless steel is similar to that of medium carbon steel, and its plasticity and toughness are high, the load is very high during cutting, and the hardening phenomenon is serious in the cutting process. The thermal difference is poor and the cutting heat is concentrated at the edge of the drill During the cutting process is easy to produce BUE, and its tissue contains a small amount of titanium carbide, resulting in bit wear quickly.
For the above questions, the following approach can be used:
A. Appropriate use of a larger feed and lower cutting speed, which is conducive to chip break, can effectively improve the life of the drill bit.
B. (2φ = 135 ° ~ 140 °), can improve the life of the drill bit.
C. When grinding the tip of the drill, the two drill edges must be symmetrical.
D. The rigidity of the machine tool and the clamping chuck is better.
E. The coolant should be sufficient.
4. Titanium alloy with a high strength, small proportion, corrosion resistance, low temperature and high temperature strength characteristics. According to the organization after annealing can be divided into α-phase titanium alloy, β-phase titanium alloy, α + β-phase titanium alloy. Α-phase titanium alloy (TA class) can not heat treatment to strengthen, so the room temperature performance is not high, with medium plasticity, machinability is acceptable. Β-phase titanium alloy by quenching aging treatment, can get a higher room temperature performance. Α + β phase titanium alloy (TC class) processing chip with the front contact length is shorter, the cutting force in the vicinity of the edge, due to the small thermal conductivity, cutting edge temperature is high, accelerated drill bit wear, and because of processing Hardening phenomenon is more serious, elastic coefficient is small, so the drilling of the larger amount of contraction, but also affect the life of the drill bit.
For the above questions, the following solutions can be used:
A. As the titanium alloy elastic deformation is large, the hole is easy to shrink, so the drill tip slightly grinding to properly increase the expansion of the hole
B. Increase the back edge of the main cutting edge and reduce the width of the cutting edge to reduce the friction between the drill bit and the hole wall.
C. In the outer edge of the corner grinding out the small vertex of the transition repair edge to improve the heat conditions (Figure 2).
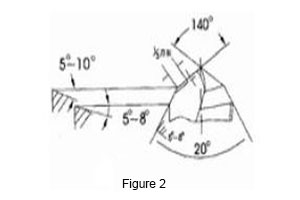
D. The main cutting edge, the appropriate reduction of the rake angle.
5. Brass a drill part is usually cast brass, which is characterized by wear resistance, corrosion resistance, but the hardness and strength is low, cutting load is small, and plasticity is poor, chip into pieces (but the pressure of brass plastic Good, chip is not broken). In the process of drilling brass often occurs "bar knife" phenomenon, that is, the drill bit automatically cut into the phenomenon, especially in the drilling will be drilled when the channel will automatically channeling, very safe, so that the hole at the exit and burr or Drill bit chipping, while the drill bit is broken.
For the above questions, the following solutions can be taken:
A. To reduce the "bar knife" problem should make the cutting edge is not sharp, so reduce the cutting edge's rake angle τ = 6 ° ~ 8 °. If the drilling pressure is machined to the brass workpiece, then τ = 10 °(see Figure 3).
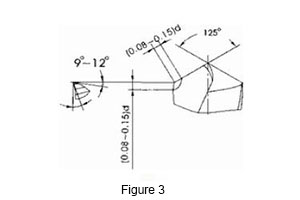
B. Grinding the blade to narrow it, but to be symmetrical, so you can drill the ideal hole.
6. Aluminum alloy - mainly cast aluminum alloy, easy to produce BUE when drilling, drilling roughness is poor, when drilling deep hole when the chip is more difficult, then the hole wall bumps, while the chip plug in the drill slot , Causing the drill to break. The elastic modulus of the aluminum alloy is small and the linear expansion coefficient is large, so the hole shrinkage occurs in the drilling hole. Casting aluminum containing silicon, silicon compounds are very hard, will make the drill wear worse. But the aluminum alloy strength is low, the hardness is low, the cutting load is small. In addition to pure aluminum, the general aluminum alloy plastic small, low elongation, so chip more smoothly.
For the above questions, the following solutions can be taken:
A. In order to prevent the hole in the drilling shrinkage, can increase the rear angle, drill tip can be slightly grinding point.
B. Drilling deep hole, the top angle can choose 2φ = 1 35 ° ~ 160 °.
Drill bit before grinding must understand the structure of the drill bit and the characteristics of the material being processed and the contradiction between the two, to understand the problems arising in the drilling, so as to be targeted to sharpen, solve the problem.
First, the processing of different materials generated problems and solutions
1. Cast iron a low hardness (usually 175-250HB), low strength, brittleness, plastic deformation is small, low thermal conductivity, the organization is loose, the chip into a crushed, drill bit wear almost all in the back, The maximum, hinder the tool life and production efficiency.
For the above questions can be the following approach:
A. The drill bit is easy to wear at the corner of the double vertex angle, so it is easy to wear and form a double vertex (see Figure 1), which increases the drill life by 1 to 2 times.
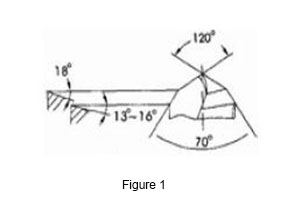
B. Appropriate increase after the angle. The outer edge of the rear edge of the use of 13 ° ~ 16 ° to reduce friction, improve the life of the drill bit.
C. Drilling to increase the feed, and appropriate to reduce the cutting speed, but not the use of high speed and small feed.
D. If the use of coolant, must not be intermittent use, while the flow should be appropriate, otherwise, the amount of small and intermittent will cause local hardening of the hole, and powder chip grinding edge will also accelerate the drill wear.
2. High-strength steel such as tool steel, carburizing steel, spring steel, bearing steel, heat-resistant steel. Drilling, drill bit cutting edge wear faster, shorter life.
For the above questions, the following approach can be used:
A Selection of high-performance high-speed steel or carbide production of the drill.
B. For hard and brittle steel, the front edge of the outer edge of the drill can be reduced to increase the strength of the edge. For steel that is hard and plastic, it does not have to be reduced.
C. Vertex angle can be used around 118 °.
D. Use phosphorus-containing cutting oil as coolant.
3. Stainless steel - generally martensitic, ferrite and austenitic three types of stainless steel. Martensitic stainless steel can resist atmospheric corrosion, good mechanical properties, the quenching and tempering treatment can improve the cutting performance, if the hardness is higher than 30HRC, the drill wear faster. Ferritic stainless steel chromium content than martensitic stainless steel, so heat treatment can not be strengthened, the cutting performance worse than the martensitic stainless steel. The mechanical strength of austenitic stainless steel is similar to that of medium carbon steel, and its plasticity and toughness are high, the load is very high during cutting, and the hardening phenomenon is serious in the cutting process. The thermal difference is poor and the cutting heat is concentrated at the edge of the drill During the cutting process is easy to produce BUE, and its tissue contains a small amount of titanium carbide, resulting in bit wear quickly.
For the above questions, the following approach can be used:
A. Appropriate use of a larger feed and lower cutting speed, which is conducive to chip break, can effectively improve the life of the drill bit.
B. (2φ = 135 ° ~ 140 °), can improve the life of the drill bit.
C. When grinding the tip of the drill, the two drill edges must be symmetrical.
D. The rigidity of the machine tool and the clamping chuck is better.
E. The coolant should be sufficient.
4. Titanium alloy with a high strength, small proportion, corrosion resistance, low temperature and high temperature strength characteristics. According to the organization after annealing can be divided into α-phase titanium alloy, β-phase titanium alloy, α + β-phase titanium alloy. Α-phase titanium alloy (TA class) can not heat treatment to strengthen, so the room temperature performance is not high, with medium plasticity, machinability is acceptable. Β-phase titanium alloy by quenching aging treatment, can get a higher room temperature performance. Α + β phase titanium alloy (TC class) processing chip with the front contact length is shorter, the cutting force in the vicinity of the edge, due to the small thermal conductivity, cutting edge temperature is high, accelerated drill bit wear, and because of processing Hardening phenomenon is more serious, elastic coefficient is small, so the drilling of the larger amount of contraction, but also affect the life of the drill bit.
For the above questions, the following solutions can be used:
A. As the titanium alloy elastic deformation is large, the hole is easy to shrink, so the drill tip slightly grinding to properly increase the expansion of the hole
B. Increase the back edge of the main cutting edge and reduce the width of the cutting edge to reduce the friction between the drill bit and the hole wall.
C. In the outer edge of the corner grinding out the small vertex of the transition repair edge to improve the heat conditions (Figure 2).
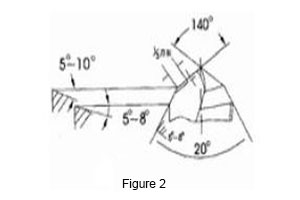
D. The main cutting edge, the appropriate reduction of the rake angle.
5. Brass a drill part is usually cast brass, which is characterized by wear resistance, corrosion resistance, but the hardness and strength is low, cutting load is small, and plasticity is poor, chip into pieces (but the pressure of brass plastic Good, chip is not broken). In the process of drilling brass often occurs "bar knife" phenomenon, that is, the drill bit automatically cut into the phenomenon, especially in the drilling will be drilled when the channel will automatically channeling, very safe, so that the hole at the exit and burr or Drill bit chipping, while the drill bit is broken.
For the above questions, the following solutions can be taken:
A. To reduce the "bar knife" problem should make the cutting edge is not sharp, so reduce the cutting edge's rake angle τ = 6 ° ~ 8 °. If the drilling pressure is machined to the brass workpiece, then τ = 10 °(see Figure 3).
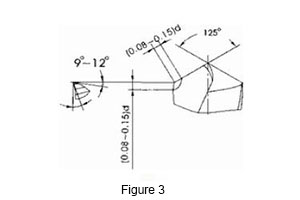
B. Grinding the blade to narrow it, but to be symmetrical, so you can drill the ideal hole.
6. Aluminum alloy - mainly cast aluminum alloy, easy to produce BUE when drilling, drilling roughness is poor, when drilling deep hole when the chip is more difficult, then the hole wall bumps, while the chip plug in the drill slot , Causing the drill to break. The elastic modulus of the aluminum alloy is small and the linear expansion coefficient is large, so the hole shrinkage occurs in the drilling hole. Casting aluminum containing silicon, silicon compounds are very hard, will make the drill wear worse. But the aluminum alloy strength is low, the hardness is low, the cutting load is small. In addition to pure aluminum, the general aluminum alloy plastic small, low elongation, so chip more smoothly.
For the above questions, the following solutions can be taken:
A. In order to prevent the hole in the drilling shrinkage, can increase the rear angle, drill tip can be slightly grinding point.
B. Drilling deep hole, the top angle can choose 2φ = 1 35 ° ~ 160 °.