Damaged carbide end mill cutter repair sharpening
Views : 734
Update time : 2017-04-13 10:54:10
1.Carbide end mill bit cutter easy broke factors
Formed carbide cutting cutters are widely used due to the small tolerance of the shape, because the blade can not be directly changed, most milling cutter can not be used after broken, which greatly improving the processing costs.
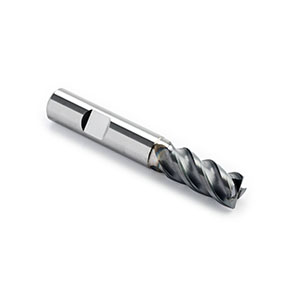
1.1 Attributes of Milling Materials
In the cutting of titanium alloy, due to the poor thermal conductivity of titanium alloy, the chip is easy to bond in the vicinity of the blade edge or the formation of BUE, in the vicinity of the tip of the knife on the formation of high temperature area, the tool red hardness loss, wear Intensified. In the continuous cutting under high temperature conditions, the binder and the weld are subject to subsequent processing of the impact, forced away from the process will take away part of the tool material, resulting in tool defects and damage. In addition, when the cutting temperature reaches 600 ℃ or more, the surface of the parts will form hardened hard layer, the tool has a strong wear effect. Titanium alloy elastic modulus is low, elastic deformation, close to the flank surface of the workpiece surface rebound, so the surface has been processed with the flank contact area, wear serious.
1.2 normal wear and tear
In the normal production and processing, when the continuous milling titanium alloy spare parts to 15mm-20mm when there will be serious blade wear situation. Continue to milling the efficiency is very low, and the workpiece surface finish is poor, can not meet the production and quality requirements.
1.3 Improper operation
Production and processing of titanium alloy casting box and the box and other processes, the clamping is unreasonable, the depth of cutting is not appropriate, the spindle speed is too fast, the cooling is not sufficient and other improper operation will lead to cutting tools, broken, broken and so on. In addition to this type of defect milling cutter can not be effective milling, but also in the milling process due to "gnawing knife" caused by the surface of the surface is depressed surface defects, not only affect the milling surface processing quality, serious cases will lead to scrap parts.
2 Improved method
2.1 cutting edge micro-collapse
Cutting edge micro-collapse (that is, slightly damaged) the most common situation, just through the grinding machine to cut the part of the cutting edge grinding off, you can re-use the tool. Grinding carbide carbide cutter should use silicon carbide grinding wheel, and can not be dipped in water grinding, otherwise the carbide will be completely scrapped due to cold cracking. The sharpening process is shown in Fig. Figure 2 for the new tool and waste cutting tool after the contrast.
After the grinding of the grinding machine, the effective length of the tool after grinding is shorter than that of the unused new tool, but this process indirectly enhances the tool rigidity, makes the processing surface quality better and improves the milling efficiency.
As the titanium alloy cast blank after forming the formation of hard and brittle uneven skin, can easily lead to chipping phenomenon, making the removal of hard skin titanium alloy processing into the most difficult process. (2mm-4mm), to control the tip of the workpiece in the surface under the hard skin is appropriate to prevent the tip of the direct contact with the crust and chipping phenomenon.
2.2 Change the tool geometry
In the tool sharpening process, you can change the tool geometry to improve the tool life, processing surface quality and cutting efficiency. Figure 3 for the head to enlarge the map.
A study of the cutting edge of the scrapped carbide cutter saw that the cutting edge of the new tool was designed to be defective, that is, the lack of transition and transition. This is the main cutting edge strength is not enough, resulting in faster tool wear, prone to "chipping" the main reason for the phenomenon.
Through the blade grinding out the arc transition plane to achieve in the cutting edge part of the addition of circular transition blade to achieve the purpose of enhancing the tip strength, both to solve the cutting edge easy to wear, easy to chipping the problem, but also improve the surface finish and milling effectiveness. While reducing the cutting edge of the cutting thickness, in a smaller cutting thickness to form a machined surface, is conducive to improving the milling surface roughness. In addition, you can also repair the grinding edge, and make it parallel to the machined surface, play a role in repairing the surface to improve the quality of the surface processing.
2.3 re-use of the waste handle
After the cutter has been repeatedly chipped and sharpened, the cutting edge portion is grinded and only the shank portion is left; or the tool is broken directly from the shank because of improper operation. In this case, you can use the remaining length of the remaining length of the handle by wire cutting, grinding, heat treatment and other methods into a single-shot, so that a single knife can be used in a safe and effective clamping range, both the use of its milling plane, , Chamfer, and can be used for boring, etc., to achieve the reusable tool waste. Figure 4 is a single knife that is processed by a scrapped handle.
In order to increase the rigidity and strength of the edge part of the end mill, the corresponding part of the heat treatment and surface coating, and the cutting part of the tool for special treatment. In view of this approach, in order to make better use of broken end mill cutter part (YG carbide) grinding into a single pole, need to heat quenching, the blade edge hardness increased to 54-57HRC, thereby improving the tool life The
After a large number of carbide scrap scissors to improve the practice and repeated use, has now formed a complete set of scrapped carbide cutter re-grinding into a single-pole process line: ① wire cutting knife handle cut; ② in the grinding machine blade Grinding the tip of the general shape; ③ edge quenching after heating into the nitrate salt after cooling, so that the hardness of 54-57HRC; ④ fine grinding out the head part, the general order of grinding: grinding blade - Face - grinding razor face - grinding out the transition blade.
3 to improve the effect
Through the manual grinding method to scrapped carbide cutter into a reusable titanium alloy material for the special cutter, the type can be divided into cylindrical cutter, ordinary single-pole, T-type single-pole and so on. According to incomplete statistics, the use of the method has been successfully sharpened forming milling cutter about 100, repeated grinding more than 1200 times, and sharpening tool life longer than the re-sharpened 2-3 times.
In the actual processing, the use of well-worn Walterφ16mm carbide end mill processing surface finish up to Ra1.6.
By analyzing the cause of the damage of the cemented carbide end milling cutter, according to the different parts of the scraped carbide cutter and the length of the available parts, the broken edge of the micro-cutting edge is increased by hand, The tool holder is reworked into a single-pole method to re-use the scrapped carbide cutter to improve service life and milling efficiency, significantly reducing processing costs.
Formed carbide cutting cutters are widely used due to the small tolerance of the shape, because the blade can not be directly changed, most milling cutter can not be used after broken, which greatly improving the processing costs.
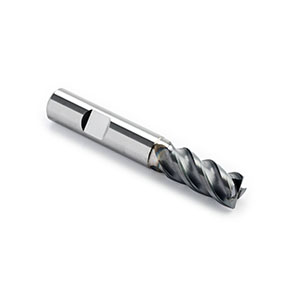
1.1 Attributes of Milling Materials
In the cutting of titanium alloy, due to the poor thermal conductivity of titanium alloy, the chip is easy to bond in the vicinity of the blade edge or the formation of BUE, in the vicinity of the tip of the knife on the formation of high temperature area, the tool red hardness loss, wear Intensified. In the continuous cutting under high temperature conditions, the binder and the weld are subject to subsequent processing of the impact, forced away from the process will take away part of the tool material, resulting in tool defects and damage. In addition, when the cutting temperature reaches 600 ℃ or more, the surface of the parts will form hardened hard layer, the tool has a strong wear effect. Titanium alloy elastic modulus is low, elastic deformation, close to the flank surface of the workpiece surface rebound, so the surface has been processed with the flank contact area, wear serious.
1.2 normal wear and tear
In the normal production and processing, when the continuous milling titanium alloy spare parts to 15mm-20mm when there will be serious blade wear situation. Continue to milling the efficiency is very low, and the workpiece surface finish is poor, can not meet the production and quality requirements.
1.3 Improper operation
Production and processing of titanium alloy casting box and the box and other processes, the clamping is unreasonable, the depth of cutting is not appropriate, the spindle speed is too fast, the cooling is not sufficient and other improper operation will lead to cutting tools, broken, broken and so on. In addition to this type of defect milling cutter can not be effective milling, but also in the milling process due to "gnawing knife" caused by the surface of the surface is depressed surface defects, not only affect the milling surface processing quality, serious cases will lead to scrap parts.
2 Improved method
2.1 cutting edge micro-collapse
Cutting edge micro-collapse (that is, slightly damaged) the most common situation, just through the grinding machine to cut the part of the cutting edge grinding off, you can re-use the tool. Grinding carbide carbide cutter should use silicon carbide grinding wheel, and can not be dipped in water grinding, otherwise the carbide will be completely scrapped due to cold cracking. The sharpening process is shown in Fig. Figure 2 for the new tool and waste cutting tool after the contrast.
After the grinding of the grinding machine, the effective length of the tool after grinding is shorter than that of the unused new tool, but this process indirectly enhances the tool rigidity, makes the processing surface quality better and improves the milling efficiency.
As the titanium alloy cast blank after forming the formation of hard and brittle uneven skin, can easily lead to chipping phenomenon, making the removal of hard skin titanium alloy processing into the most difficult process. (2mm-4mm), to control the tip of the workpiece in the surface under the hard skin is appropriate to prevent the tip of the direct contact with the crust and chipping phenomenon.
2.2 Change the tool geometry
In the tool sharpening process, you can change the tool geometry to improve the tool life, processing surface quality and cutting efficiency. Figure 3 for the head to enlarge the map.
A study of the cutting edge of the scrapped carbide cutter saw that the cutting edge of the new tool was designed to be defective, that is, the lack of transition and transition. This is the main cutting edge strength is not enough, resulting in faster tool wear, prone to "chipping" the main reason for the phenomenon.
Through the blade grinding out the arc transition plane to achieve in the cutting edge part of the addition of circular transition blade to achieve the purpose of enhancing the tip strength, both to solve the cutting edge easy to wear, easy to chipping the problem, but also improve the surface finish and milling effectiveness. While reducing the cutting edge of the cutting thickness, in a smaller cutting thickness to form a machined surface, is conducive to improving the milling surface roughness. In addition, you can also repair the grinding edge, and make it parallel to the machined surface, play a role in repairing the surface to improve the quality of the surface processing.
2.3 re-use of the waste handle
After the cutter has been repeatedly chipped and sharpened, the cutting edge portion is grinded and only the shank portion is left; or the tool is broken directly from the shank because of improper operation. In this case, you can use the remaining length of the remaining length of the handle by wire cutting, grinding, heat treatment and other methods into a single-shot, so that a single knife can be used in a safe and effective clamping range, both the use of its milling plane, , Chamfer, and can be used for boring, etc., to achieve the reusable tool waste. Figure 4 is a single knife that is processed by a scrapped handle.
In order to increase the rigidity and strength of the edge part of the end mill, the corresponding part of the heat treatment and surface coating, and the cutting part of the tool for special treatment. In view of this approach, in order to make better use of broken end mill cutter part (YG carbide) grinding into a single pole, need to heat quenching, the blade edge hardness increased to 54-57HRC, thereby improving the tool life The
After a large number of carbide scrap scissors to improve the practice and repeated use, has now formed a complete set of scrapped carbide cutter re-grinding into a single-pole process line: ① wire cutting knife handle cut; ② in the grinding machine blade Grinding the tip of the general shape; ③ edge quenching after heating into the nitrate salt after cooling, so that the hardness of 54-57HRC; ④ fine grinding out the head part, the general order of grinding: grinding blade - Face - grinding razor face - grinding out the transition blade.
3 to improve the effect
Through the manual grinding method to scrapped carbide cutter into a reusable titanium alloy material for the special cutter, the type can be divided into cylindrical cutter, ordinary single-pole, T-type single-pole and so on. According to incomplete statistics, the use of the method has been successfully sharpened forming milling cutter about 100, repeated grinding more than 1200 times, and sharpening tool life longer than the re-sharpened 2-3 times.
In the actual processing, the use of well-worn Walterφ16mm carbide end mill processing surface finish up to Ra1.6.
By analyzing the cause of the damage of the cemented carbide end milling cutter, according to the different parts of the scraped carbide cutter and the length of the available parts, the broken edge of the micro-cutting edge is increased by hand, The tool holder is reworked into a single-pole method to re-use the scrapped carbide cutter to improve service life and milling efficiency, significantly reducing processing costs.